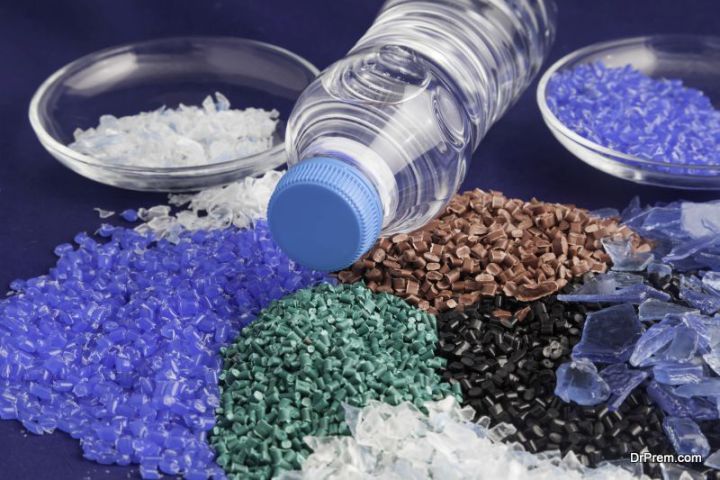
Industries taking off
The other major users of plastic materials, the construction and automotive industries, are also seeking to recover their waste. Many efforts are being made and some recycling systems have emerged in recent years.
Building industry: plastics shoot through the roof
In Europe, the building and construction industry is the second largest consumer of plastics, just behind the packaging industry. In just two decades, polymers have become essential in various sectors: wall and floor coverings, suspended ceilings, piping - pipes, tubes, fittings - insulation panels, cables, not to mention window frames and interior fittings. The advantages of fire and corrosion resistance, durability, insulating properties, low cost and aesthetics mean that plastics are now to be found on all but a few construction sites. Every year, more than 10 million tonnes of plastics are used in this industry, of which about half consists of PVC - a material which generates 1.5 million tonnes of waste every year.
PVCs loop the loop
In the late 1990s, PVC's image suffered due to the fact that, despite services rendered, it was a material that could not be recycled. PVC manufacturers then decided to set up a recycling system by encouraging collection from construction and building professionals. Launched in 2000, Vinyl 2010 aimed to recycle 200,000 tonnes of PVC in 10 years. In 2010, with 260 000 tonnes of PVC recycled in Europe, the aim was achieved and the industry set itself a new target: of reaching 800,000 tonnes a year by 2020.
At the same time, it was necessary to find solutions for recycling the most complicated items such as cables or tarpaulins. The development of the Vinyloop process was a veritable tour de force. After the waste has been ground down, it is dissolved in a solvent and the PVC is thus separated from the other materials such as copper particles, polyester fibers, natural textiles, metals, rubber, etc. The final product is pure PVC which can be used for making pipes or window frames, for instance.
Sometimes, it is the end-product manufacturers themselves who set up their own recycling systems. Thus, German window manufacturer Veka now collects PVC window frames at the end of their life cycle directly from construction sites. The frames are completely dismantled and separated into their separate components - structure, metals, joints, mounting lugs, etc. The PVC is then cleaned and crushed and the granules obtained are used in the manufacture of new PVC frames or PVC flooring.
French manufacturer Ferrari has also created its own system to recycle hundreds of square metres of its used tarpaulins through its own process called Texyloop, a proprietary technology closely resembling Vinyloop. Tarpaulins at the end of their life cycle are sorted and crushed. They are then transported to the plant in Ferrara, Italy. The tarpaulins are then placed into a selective dissolution reactor where the fibres are dissolved, filtered, cleaned and extracted. The solution is then precipitated, separating the PVC from the solvent. The solvent is then regenerated and re-injected into the recycling circuit. As for the PVC, it will find a new life in the form of waterproofing membranes, non-woven plates for insulation and even fabrics for furniture or clothing.
Automakers put the pedal to the metal
In Europe, approximately 10 million vehicles are scrapped every year. A European directive has set ambitious targets for the recycling sector. To date, 85% of the weight of an out-of-use car must be recycled, with a maximum of 5% per energy recovery. For 2015, the directive orders that the recycling rate must reach 95%, with a maximum of 10% of energy recovery. Currently, polymers represent 20% of the weight of a vehicle. The reason for this is known: plastics are lighter than metals and therefore make a significant contribution to reducing the weight of vehicles and to reducing the amount of fuel consumed by the vehicles, the latter of which is a battle that manufacturers have waged for a good thirty years. In the medium term, these same manufacturers also hope to achieve a rate of 50% following the aviation industry's model which already uses large amounts of plastics in its Airbus A350 and Boeing 787, for instance.
Like the construction industry, the automotive industry attaches increasing importance to the recycling of used plastics and especially polypropylene, a thermoplastic widely used in the automotive industry.
Recycling systems reaching maturity;
Recycling initiatives are becoming increasingly common and many new structures capable of sorting vehicle components and converting them into reusable materials are popping up all over Europe. Galloo, a Belgian company, is a leader in the field. Its strength: being one of the first to have embarked on the adventure of recycling plastics from the automotive industry and from electrical and electronic equipment (e-waste). "In 30 years, we have been able to refine our methods and to find the right solutions! We are now able to put 98% pure compounds on the market. Automotive equipment manufacturers are extremely interested in our plastics as they are primarily looking at mechanical properties and those of our recycled plastics are equivalent to those of virgin materials.
Above all, the business model of a company such as Galloo is quite viable. "Recyclers must first find a way to separate the materials present in a vehicle. The first step consists in dismantling the vehicles and sorting the parts into types: metals, glass, plastic, etc. The plastics are then ground down, regardless of their nature. After they have gone through the grinder, they emerge in the form of generally monomaterial plates measuring 5 to 6 cm because plastics parts in cars are usually made from a single polymer. Composites of various polymers are relatively rare in the used vehicles we are currently processing. Finally, these plates are placed in densitometric tables in order to separate the elements according to their density.
We have perfectly mastered this technique and we are now able to successfully separate the different polymers and then turn them into granules through an extrusion process." Galloo currently manages to recycle over 95% of a vehicle, a higher score than that required by the EU directive.
A crack team for bumpers
Manufacturers are very slowly started introducing recycled plastics into their vehicles, mainly in less visible parts such as casings. Why? For aesthetic reasons, mainly, because the intrinsic qualities of recycled plastics are essentially the same. However, in a field where the quality policy is flawless, it was inconceivable for manufacturers to use plastics not presenting perfect visual purity at the risk of offending their customers. As a result, latest generation cars contain barely 15% of recycled plastics, 80% of which is polypropylene. However, the situation is changing. In 2012, Plastic Omnium successfully designed a bumper entirely made from recycled plastic for the Peugeot 208, raising the amount of recycled plastic in the vehicle to 20%. A world first that should strongly inspire other manufacturers.