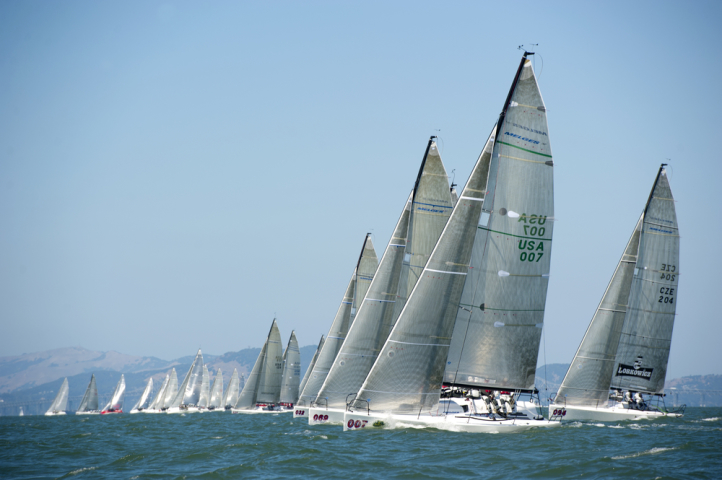
Enter performance-chasing composites
Faster, further…
Robin Knox-Johnston, Eric Tabarly, Francis Chichester, Paul Elvström...sailors all! But sailors who take part in legendary races that weekend boaters dream of. A power sport if there ever was one, ocean racing makes big demands: without a "mean machine" a sailor would have no more chance against his competitors than against the elements. It’s not rocket science – a boat has to be light to deliver performance, but it has to be strong to go the distance. Is it a matter of ‘squaring the circle’? It was until the 1980s, when a new generation of ground-breaking materials, now offered by the plastics industry in a constant drive to innovate, came on the scene.
Materials for tomorrow’s world
It was mentioned earlier that discovering new, lighter, stronger, easier to use materials is a "thing" with chemical engineers. First, because it’s a challenge they enjoy taking up, but also and especially because they know how many market opportunities and applications are out there. Coming up with a new material first and foremost means developing a fibre that, once coated with a resin, can be easily moulded. So, as early as in the 1960s/1970s, new fibres appeared on the scene, one of which, carbon fibre, would dominate the market for years.
This is rocket science !
In the 1960s, carbon fibre was still expensive to produce, which kept it the sole preserve of the still free-spending space industry. Gradually, the aviation industry would also take hold of it, followed by Formula 1. In short, carbon fibre’s new affordability, and especially its technical qualities: lightweight, high tensility compressive strength, flexibility, chemical inertness and good temperature resistance attracted manufacturers’ interest. The boating industry paid it little heed until the day when the America's Cup began to attract a huge following. Originally just a challenge for tycoons, it was to attract the cream of the racing world. Sponsors spared no expense to come up with the best possible boat. And so, in 1983, a little-known Australian swept to victory in a revolutionary yacht partly made of carbon. The race was on!
Competition still drives innovation
In boating as in other sports, competition is clearly what drives the best innovations. This is not to deny the huge part played by the talents of naval architects in designing the best aerodynamic and hydrodynamic profiles, ergonomics, rigging, etc. A talent they have successfully married to the skilful use of new materials handed to them by the plastics industry like aramids, polyethylene terephthalate, etc. Some brand names like Kevlar, Mylar, Spectra and Dyneema, all materials that are now household names to sailors, have even become generic terms.
From keel to mast
A cutting-edge competition boat is a real showcase for suppliers of composite materials which are well and truly everywhere in a racing craft. And professional competitors swear by them: the old standby, unsaturated polyester is now a thing of the past, ousted by other higher-performance materials in the drive to shed weight! That is also why synthetic fibres with mechanical strength properties that sailors value highly are now being used in the composition of textile elements like sails, ropes, etc.
To hull and back
In terms of weight, kept strictly under wraps, the latest generation of boats due to set off in a few days time on the Vendée Globe single-handed round-the-world race check in at around eight tonnes against eleven for the same type of boat 20 years ago. That is a huge weight loss and yet these ocean-going Formula 1 craft have to carry ever-taller masts (up to thirty metres) bearing 300 sq.m. of sail. Their hulls are a centimetres-thick Kevlar honeycomb structure sandwiched between super-thin carbon films - the same as those used in F1 or aerospace. In some places, the outer skin is a bare millimetre thick. The downside of this is that the thinnest points of the hull are very easily punctured, and can be holed by a single piece of metal dropped on them! Not that sailors are reckless – it is a calculated risk taken only where holing will not cause major damage. No panic, then!
Polyester fibre sailing along
A sailboat’s sails are its engine. To deliver the performance needed, a sail also has to be light, stretch-resistant and shape-holding. Another requirement is that it must withstand UV rays that will cause it to deteriorate over time. The cotton sails on the yachts of yesteryear, which were heavy and easily became water laden, have long since been replaced by synthetic materials. First up, obviously, were polyester fibres including a polyethylene terephthalate fibre discovered by two British chemists and soon after marketed by Du Pont de Nemours, now DuPont, under the trade name Dacron, the name it was introduced by to the “yachtsmen” of the 1950s. Dacron is lightweight and water-repellent. It keeps its designed shape a bit better than cotton, but still...
On the plus side, it is inexpensive and sailmakers have the designs down to a fine art. Even today, they are fitted to a very large proportion of yachts. Finally, nylon also established itself, enabling a new type of particularly high-performance sail to be developed: the spinnaker, a multi-coloured balloon-shaped sail perfect for downwind sailing. Nylon is extremely lightweight, a property essential for those in both the racing and cruising worlds who enjoy the speed and excitement of cresting the waves under an asymmetrical sail.
All brands on deck
Brand new fibres soon burst on the scene in the 1980s, attracting attention from the booming sailmaking business, always on the lookout for new innovations. Soon, the most affluent sailors were able to proudly hoist sails made of Pentex, a shape-holding Dacron derivative with low stretch properties: five percent compared to Dacron’s 15% and with good UV resistance. Mylar, a transparent film mainly used as a substrate for other fibres, would also come into use. Sandwiched between other fibres, it provides excellent sealability and near zero deformation. However, it is relatively fragile and difficult to use for large surfaces, which is why it is mainly the fibre of choice for windsurfers.
Aramids make a splash
Again, it was the 1980 America's Cup which saw these new sails unveiled to the general public. From all-white, they were now yellow or black depending on the fibre chosen. They were the hot topic of landing-stage conversation: a real technological breakthrough or just a red herring to literally put the wind up rivals? Answer: it was a real innovation! Aramids are a 100% high tech family that includes Kevlar delivering performance 25 times better than Dacron. It slashed sail weights even further. Not only that, but it holds its shape in almost all situations. On the downside, it is very sensitive to UV attack and has low bending resistance. This gives it a much shorter life, which is not good for sponsors’ pockets.
A magic solution seemed to be offered in 1983 by Spectra or Dyneema (an "ultra-high" molecular weight polyethylene), a fibre with almost twice the strength of Kevlar and ten times that of steel. It has excellent UV resistance and loses none of its properties in bending but is relatively stretchable. The perfect solution was finally found with PBO (polybenzobisoxazole), better known as Zylon and recognizable by its orange colour. This liquid crystal polymer holds its shape and is resistant to almost everything. Along with the development of these fibres came new sailmaking techniques. Previously woven, high-tech sails are now made of fibres sandwiched between plastic films, and glued or moulded. And these processes allow a three-dimensional shape to be produced, which ensures a better aerodynamic profile.
New fibres take hold of ropes and cables
It really is a no-brainer! What is a rope or a cable? A set of strands twisted about themselves. This is known as lay twist. Whatever the characteristics required: abrasion resistance, tensile strength, stretch behaviour, strain resistance, etc., manufacturers’ catalogues will always have a fibre for it. No wonder modern fibres like Spectra or Dyneema have gradually ousted hemp and cotton.
The death knell of metal
Traditional metal boat parts are on the way out. Carbon masts and booms have become standard even for weekend boaters. Stiff, strong and responsive, a carbon mast is certainly a high-performance feature, but that isn’t all it has going for it, far from it. Its low weight compared to aluminium also cuts down on the rigging: the set of cables that hold the mast. In fact this is where the most extraordinary technical developments have occurred.
Keeping a fifteen metre mast on a four-metre wide moving hull vertical is no easy task. Until recently, only steel or stainless steel could do that. But their days were numbered...Now polyurethane-coated Zylon, once again, has become the choice of elite racers for the massive lightness-gains it offers. And obviously, it is increasingly replacing metal cables.
That “Eureka” moment
More surprising still are the small plastic beads that would make American businessman Peter Harken’s fortune. As a young man in the 1960s, he developed a passion for sailing but (un)fortunately for him, he was unable to afford the steel ball bearing blocks he so craved. So he decided to make his own using plastic ball bearings which he found at his employer of the time, a medical equipment manufacturer. And surprisingly, as he himself says: "They worked great! Much slicker than greasy steel balls! Sailing friends noticed how fast my sails released, so I built pulleys for them too". The small business grew and today is a world leader on the sailboat hardware market. Plastic has obviously moved on, too, but is still very much used in Harken sailing hardware.
The long goodbye
In the old days of timber sailboats when a craft got too old to be used safely it was simply scuppered at the end of a side watercourse where it became a stock of firewood for the locals. Not a fate that can befall a plastic boat. Within the last decade, the odd few end-of-life boats started piling up on marina aprons. The question was: what to do with them? The boating industry, port managers and recycling professionals put their heads together and, looking at what the motor manufacturing industry had done, the sailing professionals set up their own system. End-of-life boats are now dismantled, the different materials sorted and recovered either by traditional recycling for timber, electrical components, some plastics and metals, or energy recycling for the rest. Given that a polyester boat has a life of around sixty years the long-term future of these businesses is assured. And that is also good news for the job market!