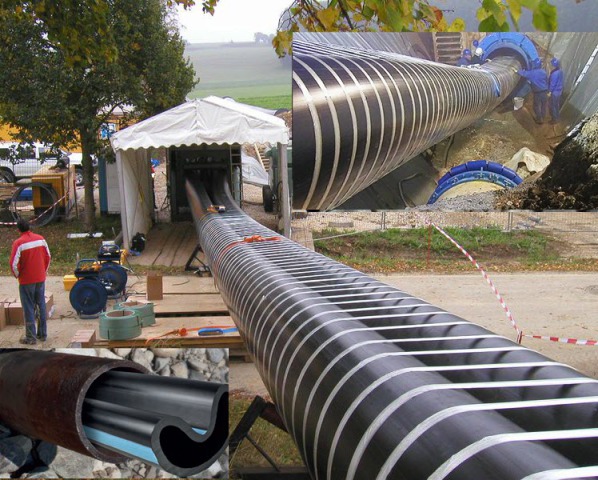
The art of preserving networks and water quality
Cast iron is getting a makeover with polymers
Although weakened by the presence of carbon in strip form, grey iron has shown an extraordinary longevity… A virtue which, sadly, has led to the ageing of the networks. Further disadvantaged by its weight and rigidity, this material has suffered from the competition with plastics.
The addition of magnesium to grey iron fortunately made it possible to correct these faults by providing the material with elasticity, along with astonishing mechanical properties. Ductile cast iron was now able to embark on a new career.
Although a major discovery, this new foundry process is not, however, the only option following its return to use in the water supply network. All manufacturers, starting with Saint-Gobain PAM, the world leader in this speciality, have also taken care to improve the surface properties of ductile iron pipes by means of polymer treatments. In some cases, the cement mortar is replaced by a thermoplastic powder coating. Other pipe systems offer internal polyurethane protection, better suited to very soft or aggressive water, while some are covered with an external high-density polyethylene coating during the extrusion of the pipes to resist very aggressive soils.
A new sleeve for old pipes
The interactions between the ground, the walls of the pipes and water are many and varied, depending on the material. Unfortunately, whatever its performance in this regard, the deterioration of the surfaces of the pipes is inevitable in the long term. Corrosion, scaling and organic deposits reduce the hydraulic efficiency of the network. Even more serious, these phenomena encourage contamination and the physico-chemical, organoleptic and bacteriological alteration of tap water.
To remedy this, the cleaning and restoration of the internal walls of the pipes is often preferable to replacing them which, in addition to new materials, requires opening trenches. One of the most efficient techniques is continuous polymerised lining. This process consists of covering the wall of the damaged pipe with a synthetic membrane impregnated with epoxy resin or polyester that hardens after polymerisation. Less intrusive and quicker, this renovation operation makes it possible to limit the nuisance of working sites and interruptions to the use of the network.
The plastic pipe keeps its shape
The old sections of the water supply system sometimes suffer severe deterioration that, as well as the surfaces, affects the very structure of the pipes. In addition to risks of breaches, their cracking constitutes a threat to watertightness and, therefore, a risk of polluting the drinking water within.
In this context, the process of renovating damaged pipes with plastic piping offers the best alternative to replacing them. The simplest method is to introduce a new soft polyethylene tube into the existing pipe. The only problem is that reducing the diameter of the pipe sometimes forces network managers to use more sophisticated techniques.
Tubing without an annular space, for example, makes it possible to install an HDPE pipe of the same diameter as the old one after fracturing or levelling it. The elasticity of the polymer facilitates the insertion of the new pipe, which is arched in mechanically or folded into an ‘U’ shape before it resumes its cylindrical shape due to the injection of water or hot air under pressure.
New synthetic lining for Montmartre reservoir/h2>
The effective performance of the drinking water systems depends on more than the state of the pipes. Discreet and well protected, drinking water reservoirs also play a crucial role. These subterranean and rather mysterious constructions, sometimes used as locations for spy films, are more vulnerable to the ravages of time than to human intrusions.
In 2013, the Montmartre reservoir, built in 1889 on the slope of the Sacré-Cœur, showed signs of degradation, posing a long-term threat to the watertightness of the facility and the quality of the water supply. At that point, even a traditional polymer resin lining would have been unable to repair the damage.
The Paris Water service therefore opted for an innovative process developed by the Austrian plastics firm Agru, specialists in water pipe systems. This solution meant that the walls of the reservoir could be covered with an inner shell composed of high density polyethylene (HDPE) sheets welded on a surface area of 2,200 m2. This is of twofold interest for sites built out of concrete. The sheets are perfectly smooth on the side in contact with the drinking water, thus avoiding organic deposits, but they are fitted with small flexible pins on the reverse side to absorb deformations in the concrete and drain away possible infiltrations through the original wall.